Organic fertilizer production processes are using livestock and poultry manure which is different from the production of other fertilizer products. To make full use of organic components in the manure, the production process forms effective organic fertilizer for the soil. In this process, Shunxin as a professional fertilizer production machine manufacturer, can provide customers different types of manure processing machines.
There are many kinds of organic fertilizer products according to different raw materials processed by various production processes. Here are some organic fertilizer production projects from Shunxin facility in several countries to be combined with. Let’s take a brief walk-through of the production processes of various organic fertilizers from different organic materials.
Process overview for organic fertilizer making
The Composting process for raw organic material and the Fertilizer Production process for the composted material are the 2 main parts of an organic fertilizer production process. Then the subsequent processes are deep processing and commercialization for the organic fertilizer products. The fertilizer business owner can choose a suitable plan according to his/her fertilizer production need.
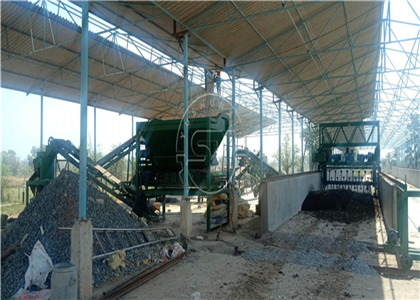
Shunxin Chicken Manure to Powder Organic Fertilizer Production Line in India
For example, the composted material can be treated into powder organic fertilizer products in a Powder Organic Fertilizer Fertilizer Production Line, like the our chicken manure to powder organic fertilizer project in India shown as in the above picture; or the fermented manure can be processed into granular organic fertilizer using granulator equipment in a Granulator Organic Fertilizer Fertilizer Production Line, like our cow dung to granular organic fertilizer project in Myanmar shown as in the below picture.
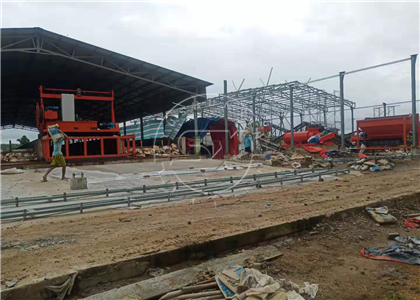
Shunxin Cow Dung to Granular Organic Fertilizer Project in Myanmar
Processing for watery material
Taking different kinds of raw material into consideration, the processes before the composting are not quite the same. If the material is with too much water in it, the composting will be highly affected. A better option is to use Shunxin Solid-liquid Separator to dehydrate the raw watery material.
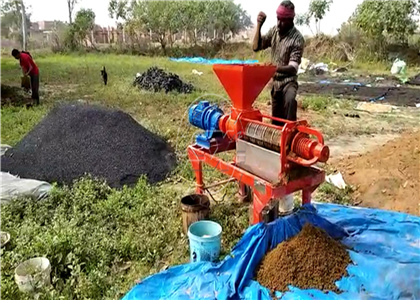
Shunxin Dewatering Machine performs well for Myanmar customer
Before the composting process of Chicken manure organic fertilizer production
Chicken manure usually has a high moisture content, and chiken litter fertilizer production process can be applied to all other poultry manures’ treatment. At the first stage of composting/fermentation treatment in the organic fertilizer production, different kinds of raw materials with too much water content are not suitable for compost or fermentation, and the best way to proceed is to perform the dehydration treatment to them. You can use a chicken manure dehydrator to separate the solid matter from the watery manure material, and then start the composting/fermentation to make the material rot.
On the composting process of Cow dung organic fertilizer production
Some raw material of cow dung needs to be dehydrated as well if it contains a lot of urine or water. Due to the different foods fed to the different cows, the digestibility among the cow herd is also very different. Cow dung is well known for its containing more fiber components, relatively speaking, the water content within cow dung material is relatively moderate and suitable, which is very helpful for composting or fermentation treatment. It’s worth noting that the composting processing period for such raw manure material with a water content higher than 60% should last slightly longer than normal so as to ensure the raw cow dung material is thoroughly rotted. (Related page about cow dung disposal, wlecome to how to make cow dung fertilizer.)
About the Biogas residue organic fertilizer production process
Biogas residue is the residue remaining after the production of biogas from livestock manure, and it is a very good kind of raw material for the production of microbial organic fertilizer. Although the biogas residue has been anaerobic fermentation, in order to completely achieve harmlessness, it is still necessary to continue to enter the tank for aerobic fermentation. The biogas residue extracted from the biogas digester has a high water content, which is the same as chicken manure. It needs to be dehydrated and then composted for the organic fertilizer production process.
How to compost raw manure material
To start an organic fertilizer production process, the raw material of organic matters has to be completely composted/fermented before the final fertilizer production process. The aerobic fermentation method is widely applied for the organic material composting process. You can stack your raw material into piles or put it into the channels or the composting area for the composting process as below.
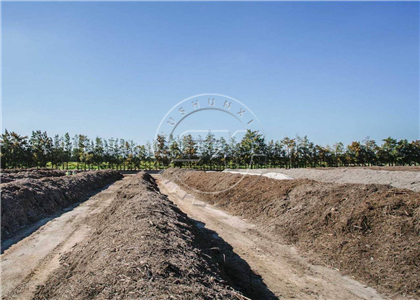
Small scale of raw organic material stacked as piles for composting
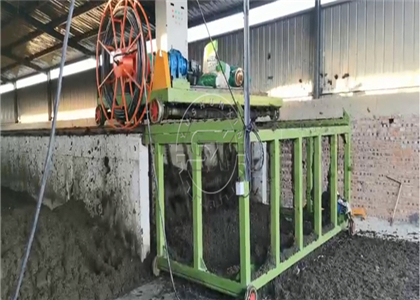
Composting process in the channel for medium capacity of raw material
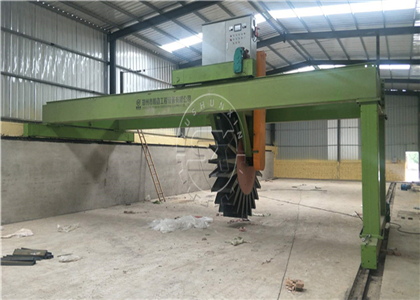
Large amount of raw organic manure being composted
You will get suggested with the most suitable composting machines according to your material amount for composting from Shunxin Tech Team. After applying the Shunxin Organic Material Composting Turner as instructed, you will get well-fermented organic material compost fast within about 20 days.
4. Processes for organic fertilizer production
After the composting process is completed, the original organic materials have been fully processed into compost, which can be used for organic fertilizer production.
For Powder Organic Fertilizer Production Process
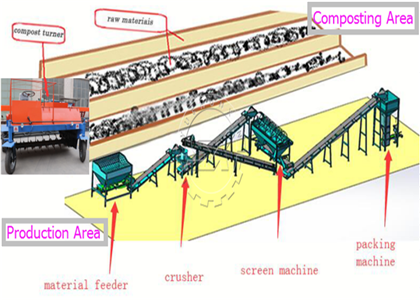
A. You will move the compost into the first Feeding process in the Production area from the Composting area. This is for feeding the compost to the following process steadily and continuously;
B. The belt Conveyor will convey the compost to the next Crushing process. This is to crush the large particles not cracked down during the composting into fine powder;
C. The Screening process is used to make sure all the compost is in powder state for the next process. Any uncrushed big particles or hard lumps will be screened out back for re-crushing;
D. All fine powder compost comes to the Packing process to be bagged automatically and quantitatively as planned for commercial usage.
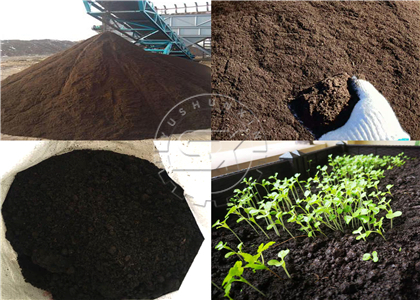
For Granular Organic Fertilizer Production Process
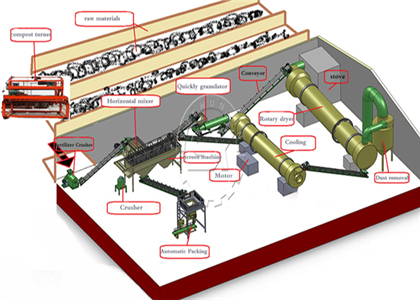
A. Same processes as in the Powder Organic Fertilizer Production Process for the compost from the Composting area to the Feeding + Crushing + Screening processes in the Production area;
B. The screened powder compost goes into the Mixing process for additives and/or some other ingredients as needed to improve the nutrients of the final fertilizer. The powder moisture in this process needs to be increased to about 30~40% for better granulation;
C. The Granulating process will make the mixed powder into uniform granules and discharge them to the next process;
D. The temperature of the granules will rise up to about 50~60℃ in the Drying Process. So that the increased moisture can get dried out to about 8~10%;
E. The Cooling process will cool down the temperature of the dried granules to normal level;
F. There may be some powder compost that failed the granulation, and some granules are broken during the drying/cooling process. The Screening process will remove the unqualified back for re-crushing and re-granulating.
G. Finally the round cooled granules arrive at the Packing process for commercial bagging.
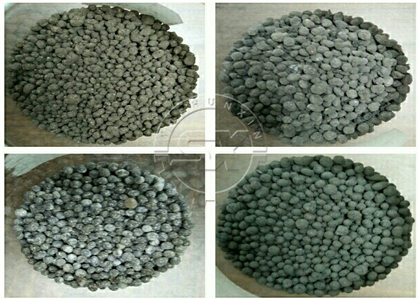
5. Special process design for your organic fertilizer production
The production processes of organic fertilizers are not always fixed. We can make corresponding adjustments according to your specific requirements.
For example, during the composting process, you find that your raw material contains a lot of hard-to-crush stones and even iron blocks. We can first screen the compost and add a Metal Clearing Device to remove the harmful components, then take it to crush.
Or you plan to coat the final granules to a better looking and longer storage, we can set up a Coating process after the Cooling. No matter powder coating or liquid coating, we can update the project design as you need.
Want to know more about the organic fertilizer production process? Come on and leave us your idea about the fertilizer producing project. Let’s make a perfect organic fertilizer production plan for you!